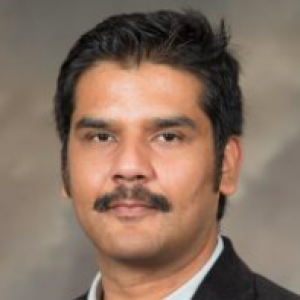
Bishal Silwal
Assistant Professor, Department of Mechanical Engineering Georgia Southern University
- Statesboro GA
Bishal Silwal is an expert in Welding and Joining, Arc Based Additive Manufacturing, and Transport Phenomenon in Material Processing.
Social
Biography
Areas of Expertise
Education
Utah State University
Ph.D.
Articles
Effect of vibration and hot-wire Gas Tungsten Arc (GTA) on the geometric shape
Journal of Materials Processing TechnologyB. Silwal et al.
2017
Bead-on-plate experiments were carried out, and the weld-bead size and shape were compared and discussed. The welding droplet parameters were measured by a high-speed camera. A computation fluid dynamics (CFD) model utilizing VOF (volume of fluid) method, incorporating the experimental droplet parameters has been developed to understand the weld pool dynamics and subsequent weld pool geometry. From the experimental results, a narrower and deeper penetration was observed with hot-wire while wider and shallow penetration was observed with cold wire gas tungsten arc welding (GTAW). The developed model has been applied to predict and analyze the mechanism for narrower and deeper penetration. A modified relationship has been established for droplet detachment in hot wire GTAW.
Creep rates of heat-affected zone of grade 91 pipe welds as determined by stress-relaxation test:
Creep rates of heat-affected zone of grade 91 pipe welds as determined by stress-relaxation testB. Silwal et al.
2016
Cross-weld creep testing conducted at 650 °C under 69 MPa stress has reproduced either the Type I or Type IV failure mode in Grade 91 welds, depending on the post-weld heat treatment procedures. Welds post-weld heat treated below the AC1 temperature have ruptured in the Type VI failure mode, while welds heat-treated above the AC1 temperature of the alloy have ruptured in the Type I failure mode. Heat-treatments at lower temperatures and shorter durations have produced a reduced creep rate. The accelerated short term stress-relaxation test has been conducted to obtain the input creep rates for a finite element model for the cross-weld creep testing. The model predicted secondary creep rates are in good agreement with the results from the conventional cross-weld creep tests. From the finite element model, the creep damage by cavitation is believed to start at regions where the first principal stress and stress triaxiality concentrate.
Effect of Post-weld Heat Treatment on Toughness of Heat-affect Zone of Grade 91 Steel
Welding JournalB. Silwal et al.
2013
The impact toughness of the heat-affected zone (HAZ) for Grade 91 steel welds has been experimentally investigated. The as-welded multipass HAZ has a significant scatter in toughness, due to variations in the Charpy notch location and the path of fracture propagation. The cross-weld Charpy specimen gives a toughness value that can be attributed to contributions by the weld metal, various HAZ regions, and the base metal. The microstructure evolution of various HAZ regions during postweld heat treatment (PWHT) has been investigated and used to explain the toughness changes. A 760° for 2 h PWHT can significantly increase the cross-weld toughness of the HAZ. The measured weld HAZ toughness can be understood using a linear additive model that employs as the inputs the toughness values of various HAZ regions reproduced on the Gleeble® The toughness of the coarse-grained heat-affected zone (CGHAZ) recovers the slowest as a function of increasing PWHT temperature, and remains low until a 730° heat treatment. To guarantee an adequate HAZ toughness, a PWHT of at least 730° is recommended. Postweld heat treatment above the A C1perature will result in the formation of fresh martensite, which decreases the toughness and increases the hardness of all HAZ regions. Postweld heat treatment 20° below the AC1 temperature for 2 h has produced the highest toughness and lowest hardness of all HAZ regions.