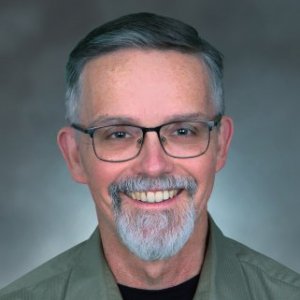
Daniel Williams, Ph.D.
Associate Professor Milwaukee School of Engineering
- Milwaukee WI
Dr. Daniel Williams research interests are in dynamic systems modeling, control system design and fluid power.
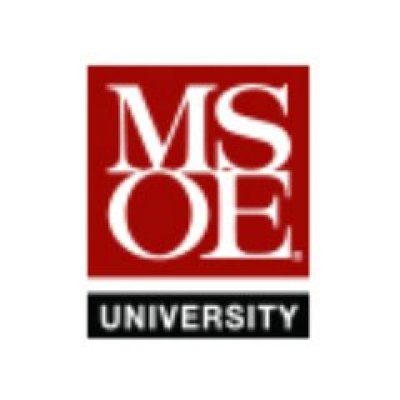
Milwaukee School of Engineering
View more experts managed by Milwaukee School of Engineering
Education, Licensure and Certification
Ph.D.
Mechanical Engineering
University of Wisconsin-Madison
1990
M.S.
Mechanical Engineering
University of Wisconsin-Madison
1986
B.S.
Mechanical Engineering
University of Wisconsin Platteville
1982
Biography
Areas of Expertise
Accomplishments
Deere & Company Innovation Award
India Backhoe Fuel Economy
Deere & Company Inception Contest Finalist
Towing Power Amplifier
Social
Media Appearances
FLAME Project introduces girls to mechanical engineering
MSOE News
2018-12-20
Girls toured MSOE’s laboratories and heard from faculty and students about the different career opportunities that are available to mechanical engineers. They also had the opportunity to put their own skills to the test in a team-based engineering challenge. Students built a pneumatic arm out of Legos and hoses that was tasked with moving sponges from a board into an egg carton. Dr. Daniel Williams, an associate professor in the Mechanical Engineering Department, devised the design challenge.
Motion Control Lab upgrades offer enhanced learning
MSOE News
2018-11-14
“Modern advances in sensors and electronic controls have enabled fluid power systems to evolve, becoming more effective at what they do and more efficient in how they do it,” said Dr. Daniel Williams, associate professor, Mechanical Engineering Department. Williams, whose resume includes John Deere and Snap-on Tools, brings 20 years of industry experience to his post. “In the Motion Control Lab, students learn about the challenges involved in employing a real-world fluid power system and the opportunities to overcome those challenges with state-of-the-art computer control.”
Event and Speaking Appearances
Intermediate Hydraulic Systems
John Deere Construction & Forestry Division and John Deere Cylinder Division. 2019
Deere & Company Linking Engineering Technical Specialties Conference
Multiple annual presentations on dynamic systems simulation
Modeling for Advanced Decision Making in Product Development
2000 EASY5 User’s Conference Guest Speaker
Analytical Evaluation of Off-Road Machine Concepts Using EASY5®
Eurotex European Union - Texas Joint Workshop On Advanced Design Technologies Dallas, Texas, April, 1999
Patents
Semi-active ride control for a mobile machine
US7165395B2
2007
A system and method of achieving ride control for a work vehicle that replaces a traditional accumulator with a ride control valve, a directional control valve and a fluid pressure source. The fluid pressure source may be a variable displacement hydraulic pump. The ride control valve is set to a first relief pressure that allows fluid to flow from the head end of a hydraulic cylinder when the loading on the cylinder, i.e., the pressure in the head end is equal to or greater than the first relief pressure. A work tool of the vehicle falls from a first position to a second position when fluid flows from the head end. The ride control valve is then reset to a second relief pressure, higher than the first relief pressure and sufficient to move the work tool toward the first position. Afterwards, the directional control valve is opened long enough to allow fluid from the fluid pressure source to enter the head end and move the work tool back to approximately the first position. The ride control valve may be dynamically adjusted.
Wire stub retainer and handle opening spring
US4627164A
1986
A clip-like, resilient wire stub retainer and handle opening spring adapted for secure positioning on the pivoting joint area of a wire cutting pliers having a pair of cutting edges extends along a first cutting edge of the pliers in an overlapping manner so as to engage and retain a severed wire stub portion in contact with a second cutting edge of the pliers until the pliers are released in preventing the wire stub from being projected away from the pliers. The resilient clip-like retainer/spring biases the pliers to the open configuration and includes a sheath-like covering on the wire engaging portion thereof to enhance its wire retention characteristics.
Selected Publications
Simulation-Based Experiments in Hydraulic Motor Speed Control
National Fluid Power Association – Education and Technology FoundationDaniel W. Williams 2022
The intent in preparing this document is to guide the reader in using the accompanying MATLAB files (Simulink models and associated parameter scripts) to run simulation-based experiments on a model of a hydraulic motor speed control circuit. The hydraulic circuit under consideration represents one configuration of the fluid power test stands located in MSOE’s Motion Control Lab. This lab facility is used for the required course in automatic control systems.
With the social-distancing constraints associated with the COVID-19 pandemic, students were afforded only minimal time is the physical lab. In response to this reality, simulation-based experiments were used to give the students an opportunity to conduct the full laboratory exercises on their personal computers. The simulation model of the physical setup provided a sufficient degree of realism for the students to experience many of the issues normally associated with the equivalent physical lab, albeit without the sights and sounds of the real machinery.
Development of a Motion Control Laboratory Focusing on Control Design and Fluid Power Education
ASEE Annual Conference and ExpositionRodriguez, Luis A, Williams, Daniel, and Cook, Michael D.
2019
This paper presents the development of a Motion Control Laboratory in the department of Mechanical Engineering at Milwaukee School of Engineering (MSOE). The main objectives of the lab are to 1) Prepare students to work in real-world motion control applications by providing students with hands-on experiences to better understand control system design ideas and concepts, 2) Expose students to electromechanical and fluid power hardware, and 3) Educate students about the benefits and capabilities of fluid power and electromechanical actuation. Students analyze systems in both open-loop and closed-loop operation, implement simulations validated by experimentation, and perform control system design. Hands-on laboratory experiences are used to reinforce control system concepts, introduce students to fluid power and electromechanical hardware, and provide experience with real-time control and industrial strength hardware. The lab experiences begin with a structured inquiry format investigation into numerous control strategies and culminate with an open-ended design lab experience where the students design a closed-loop controller of their choice to meet a set of desired design specifications. This allows students to connect how abstract concepts lead to the realizable control of hardware. Outcomes of a student exit survey are used to provide recommendations for future improvement in class offerings.
An inverse kinematic analysis procedure for flexible open-loop mechanisms
Mechanism and Machine TheoryDaniel W. Williams, David A. Turcic
1992
This paper presents the development of a point-oriented kinematic analysis procedure for open-loop mechanisms that includes provision for elastic links. The analysis method is based upon specifying the three-dimensional reference locations of control points that lie at specified locations on the mechanism. An iterative method based upon 4 × 4 transformation matrix techniques is utilized to solve for the values of the joint variables that define the configuration of the mechanism as well as their velocities and accelerations. This is first done with the assumption that the mechanism links are rigid in order to determine the nominal mechanism state for load calculation purposes. Quasi-static loading conditions are assumed in order to calculate the deformed shapes of the links which are then used to reiterate on the position analysis. The method incorporates least-squares to allow the solution when the control point data is underspecified, overspecified or inconsistently specified. Examples are provided in which the analysis procedure incorporating elastic links is applied to the solution of two planar manipulator positioning problems.