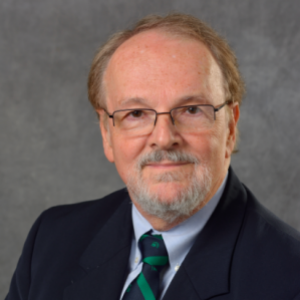
Lawrence Drzal
University Distinguished Professor of Chemical Engineering and Materials Science Michigan State University
- East Lansing MI
Expertise in adhesion, surface modification, composites/nanocomposites, graphene nanoplatelets, and multifunctional materials.
Biography
Dr. Drzal is a University Distinguished Professor of Chemical Engineering and Materials Science at Michigan State University. He is Director of the Composite Materials and Structures Center at MSU, an interdisciplinary research center focusing on all aspects of polymeric, composite materials and their processing. He was co-Director of the NSF State/Industry/University Center for Low-Cost, High-Speed Polymer Composites Processing. From 2015 to 2018 he was the Vehicle Application Director of the Institute of Advanced Composite Manufacturing Innovation (IACMI).
Dr. Drzal is a founding member of the Adhesion Society (President 1998-2000) and the American Society for Composites. In 2007, Dr. Drzal co-founded XG Sciences, Inc, a private Michigan company that is the world’s largest manufacturer of graphene nanoplatelets using processes and technologies developed at MSU. XG Sciences currently has 50+ employees. He serves as its Chief Scientist.
Industry Expertise
Areas of Expertise
Accomplishments
Lifetime Achievement Award
2016
Awarded by the Society of Plastics Engineers, Automotive Division.
Medal of Excellence in Composite Materials
2016
Awarded by the University of Delaware
Membership
2015
National Academy of Inventors
Education
Case Western Reserve University
Ph.D.
Chemical Engineering and Polymer Science
1974
University of Detroit
B.S.
Chemical Engineering
1967
News
University of Delaware Announces Composite Medal Award Winners
Composites World
2016-05-23
The Medal of Excellence in Composite Materials was established in 1984 in conjunction with the Decennial Celebration of the Center for Composite Materials of the University of Delaware. The medal is to recognize outstanding achievement in the field of composite materials. The medal carries the names and likenesses of the four initial recipients of the award: Dr. Zvi Hashin, Dr. Tsuyoshi Hayashi, Dr. Anthony Kelly and Dr. Stephen W. Tsai.
Second Location Announced for MSU-led Composite Materials Institute
MSU Today
2015-09-18
Creation of the institute was announced earlier this year by President Barack Obama. Sharing the stage with the president for the announcement was Lawrence Drzal, director of MSU’s Composite Materials and Structures Center.
Drzal, a University Distinguished Professor of chemical engineering and materials science, is serving as director of the IACMI’s Michigan Center of Excellence...
Obama: Michigan State to Take Major Role in Developing Crucial Lightweight Materials in Autos
Michigan Live
2015-01-12
Michigan State is the home of the Composite Materials and Structures Center and the Composite Vehicles Research Center. Lawrence Drzal serves as the director of the Composite Materials and Structural Center and will serve in a leadership position in the new consortium. as the director of the Michigan Center of Excellence. He shared the stage with Obama during his speech in Knoxville.
“These two world-class facilities will serve as the foundation for future work in this program,” Drzal said in a statement. “We’re confident the IACMI will create new jobs, support the expansion of companies and educate technicians and engineers for these industries.”...
MSU Assumes Leadership Role in National Composite-Materials Venture
MSU Today
2015-01-09
“These two world-class facilities will serve as the foundation for future work in this program,” said Lawrence Drzal, director of the MSU Composite Materials and Structures Center, who will serve as director of the Michigan Center of Excellence for the newly formed institute. “We’re confident the IACMI will create new jobs, support the expansion of companies and educate technicians and engineers for these industries."...
New Nanomaterial Makes Plastic Stiffer, Lighter And Stronger
Science Daily
2008-08-15
The material – xGnP Exfoliated Graphite NanoPlatelets – will be instrumental in the development of new and expanded applications in the aerospace, automotive and packaging industries, said Lawrence Drzal, University Distinguished Professor of chemical engineering and materials science at MSU and director of MSU’s Composite Materials and Structure Center...
Journal Articles
Nanoscale toughening of carbon fiber reinforced/epoxy polymer composites (CFRPs) using a triblock copolymer
Polymer2017
This work explored the incorporation of a triblock copolymer in carbon fiber reinforced epoxy polymer composites (CFRPs) to improve their mode-I fracture toughness, GIc (J/m2). The triblock copolymer poly (styrene)-block-poly (butadiene)-block-poly (methylmethacrylate) (SBM) was used to modify the CFRP matrix at 5, 10 and 15 phr concentrations, respectively. CFRPs were manufactured using an in-house sizing tower system, prepregger, vacuum bag and autoclave method. Mode-I fracture toughness testing revealed a 290% increase in GIc by incorporation of the reactive sizing on the fibers and 10 phr SBM in the matrix. Scanning electron microscopy of the SBM modified CFRP fracture surfaces showed that well distributed, sub 100 nm spherical micelles of SBM underwent cavitation and induced void growth and shear yielding toughening mechanisms to absorb fracture energy. It is noteworthy that longitudinal and transverse composite three point flexural testing showed that the SBM modified matrix did not decrease CFRP strength and stiffness up to 10 phr additive. Further, dynamic mechanical analysis revealed that SBM at 10 phr decreased the glass transition temperature (Tg) of CFRPs by only 2.9 °C; the Tg was then recovered at 15 phr SBM. Finally, the SBM modified CFRP GIc was compared to the neat matrix GIc at 0, 5, 10 and 15 phr SBM to develop a ‘transfer factor’ for SBM modified composites. It was found that only 10% of the increased matrix toughness was transferred from the SBM modified epoxy to the CFRPs. The presence of the rigid carbon fibers constrains plastic deformation of the modified epoxy and limits the toughness transfer in the composite.
Interlaminar reinforcement of glass fiber/epoxy composites with graphene nanoplatelets'
Composites2015
This work investigated the ability of graphene nanoplatelets (GnPs) to improve the interlaminar mechanical properties of glass-reinforced multilayer composites. A novel method was developed for the inclusion of GnPs into the interlaminar regions of plain-weave, glass fabric fiber-reinforced/epoxy polymer composites processed with vacuum assisted resin transfer molding. Flexural tests showed a 29% improvement in flexural strength with the addition of only 0.25 wt% GnP. At the same concentration, mode-I fracture toughness testing revealed a 25% improvement. Additionally, low-velocity drop weight impact testing showed improved energy absorption capability with increasing concentration of GnPs. Ultrasonic C-scans and dye penetration inspection of the impact- and back-sides of the specimens qualitatively support these results. Finally, the impact damage area was quantified from the C-scan data. These results showed that the impact-side damage area decreased with increasing concentration of GnP, while the back-side damage area increased.
Mechanical and electrical properties of carbon fiber composites with incorporation of graphene nanoplatelets at the fiber-matrix interphase'
Composites2015
In this study, carbon fibers (CFs) were coated with graphene nanoplatelets (GnP), using a robust and continuous coating process. CFs were directly immersed in a stable GnP suspension and the coating conditions were optimized in order to obtain a high density of homogeneously and well-dispersed GnP. GnP coated CFs/epoxy composites were manufactured by a prepreg and lay-up method, and the mechanical properties and electrical conductivity of the composites were assessed. The GnP coated CFs/epoxy composites showed 52%, 7%, and 19% of increase in comparison with non-coated CFs/epoxy composites, for 90° flexural strength, 0° flexural strength and interlaminar shear strength, respectively. Meanwhile, incorporating GnP in the CF/epoxy interphase significantly improved the electrical conductivity through the thickness direction by creating a conductive path between the fibers.
Multifunctional graphene nanoplatelets/cellulose nanocrystal composite paper'
Composites2015
We demonstrate a water-based method to fabricate strong, electrically and thermally conductive hybrid thin films (papers) made from the combination of graphene nanoplatelets (GnP) and cellulose nanocrystals (CNC). Unpressed and hot-pressed GnP papers containing CNC ranging from 0 wt% to 25 wt% were prepared. It is found that the GnP is well aligned within the hybrid paper, and a higher degree of alignment is induced by the hot-pressing process. The mechanical properties of the resulting papers increased with increasing content of CNC. The hot-pressed 25 wt% CNC hybrid paper showed the best mechanical properties among all the papers studied and improved the tensile strength by 33% and the modulus by 57% compared to neat GnP paper. Both the highest in-plane and though-plane thermal conductivity of 41 W/m K and 1.2 W/m K were measured respectively for the hot-pressed 15 wt% CNC hybrid paper. The electrical conductivity decreased continuously with increasing content of CNC but the thin film was still conductive at the highest CNC content in this study. The low-cost, environmental-friendly, thermally and electrically conductive flexible GnP/CNC hybrid papers have a set of properties making them suitable for many potential applications.
Mechanical properties and thermal conductivity of graphene nanoplatelet/epoxy composites
Journal of Materials Science2015
Nanocomposites of epoxy with 3 and 5 wt% graphene nanoplatelets (GnPs) were fabricated with GnP sizes of ~5 and