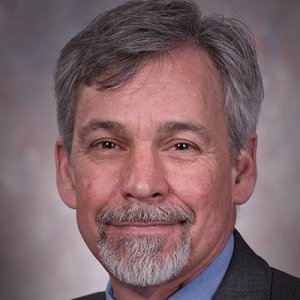
Paul Michael
Director of Fluid Power Institute Milwaukee School of Engineering
- Milwaukee WI
Paul Michael's area of expertise is in tribology: the science of friction, lubrication and wear.
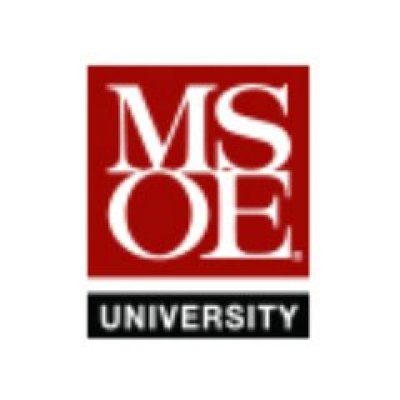
Milwaukee School of Engineering
View more experts managed by Milwaukee School of Engineering
Education, Licensure and Certification
M.B.A.
Keller Graduate School of Management
DeVry University
B.S.
Chemistry
University of Wisconsin‐Milwaukee
Biography
Prior to joining MSOE, Michael was the technical director of Benz Oil and a laboratory manager for Filmite Oil.
Areas of Expertise
Accomplishments
Edmond Bisson Best Paper Award, Society of Tribologists and Lubrication Engineers (STLE)
2020
Fluid Power Motion Control Conference Best Paper Award, American Society of Mechanical Engineering (ASME)
2019
Otto J. Maha Pioneer in Fluid Power Award, Milwaukee School of Engineering (MSOE)
2012
Karl O. Werwath Engineering Research Award, Milwaukee School of Engineering (MSOE)
2011
Award of Appreciation, American Society for Testing and Materials (ASTM)
2008
Outstanding Contributor to Standards Development, National Fluid Power Association (NFPA)
2005
Affiliations
- ASTM: Co-chair, Hydraulic Fluid Thermal Stability Compatibility Section D02.N0.15
- ISO: Committee Fluid Power Product Testing Section TC 131 SC6
- NFPA: Technical Board
Social
Media Appearances
Technology makes hydraulic reservoirs more efficient
Design World
2015-06-08
DW: Paul, can you tell us how MSOE got involved and then the results of your investigation on HydroNucleation technology?
Michael: Helgesen Industries contacted MSOE’s Fluid Power Institute in order to investigate the feasibility of the HydroNucleation technology. We received two reservoirs from Helgesen, one with a standard technology and another with the HydroNucleation technology incorporated. We ran a series of tests with the axial-piston pump and the HydroNucleation reservoir at different temperatures, speeds, pressures, and so on—and compared the efficiency of the pump with the two different reservoir technologies as well as the maximum flow rate and aeration levels of the reservoir.
Selected Publications
Critical Shear Rate of Polymer-Enhanced Hydraulic Fluids
Lubricants, Vol. 8, No. 12Panwar, P. Michael, P. Devlin M. and Martini, A.
2020
Fluid Property Effects on Power Consumption in a Hydraulic System at Low Temperatures
Proceedings of the ASME/BATH 2020 Symposium on Fluid Power and Motion ControlMichael, P. Dai, C. and Rodriguez, K.,
2020-09-09
Paper FPMC2020-2747
Hydraulic Fluids
ASTM Fuels & Lubricants Handbook: Technology, Properties, Performance and Testing, G.E. Totten Ed., ASTM InternationalMichael, Paul and Zhao, Hongmei
2019
Fluid Effects on Mechanical Efficiency of Hydraulic Pumps: Dynamometer Measurements and Molecular Simulations
Proceedings of the ASME/BATH 2019 Symposium on Fluid Power and Motion ControlPanwar, P. Len, M. Gajghate, N. Michael, P. and Martini, A.
2019-10-07
Paper FPMC2019-1712 - Best Paper Award
Empirical Modelling of Hydraulic Pumps and Motors based upon the Latin Hypercube Sampling Method
International Journal of Hydromechatronics, Vol. 1, No. 3Panwar, P. and Michael, P.
2018
Temporary and Permanent Viscosity Loss Correlated to Hydraulic System Performance
Tribology TransactionsMichael, P., Cheekolu, M., Panwar, P., Devlin, M., Davidson, R., Johnson, D., Martini, A.
2018
Straight- and multi-grade fluids were evaluated in a hydraulic dynamometer that incorporated a pressure-compensated axial piston pump and a fixed displacement axial piston motor. Pump, motor, pressure compensator and directional control valve internal flow losses were determined under various conditions of pressure, speed and temperature. Fluid samples were collected before and at various times during the dynamometer experiments, and viscosity measurements were performed to probe for correlations between viscosity, operating time and system leakage flow losses. The low-shear rate viscosities of the multi-grade fluids decreased linearly through the duration of testing due to polymer degradation. However, system flow losses did not exhibit a statistically significant increase as the multi-grade fluids sheared down. The fluids were also characterized by their permanent viscosity loss produced in sonic and tapered bearing tests and by their temporary shear thinning measured in an ultra-high shear viscometer at several temperatures. The effects of these viscous properties on flow loss were analyzed using an empirical model to identify which measures of viscosity were most correlated to efficiency. The results suggested that the relative contributions of temporary and permanent viscosity loss change as the fluid is used. Further, analysis of torque loss and input power revealed that input power and losses are more useful indicators of the effect of fluids on hydraulic system performance than pump efficiency.
An Investigation of Hydraulic Fluid Composition and Aeration in an Axial Piston Pump
Conference: ASME/BATH FPMC Symposium on Fluid Power and Motion Control, At Sarasota, FLGullapalli, S., Michael, P., Kensler, J., Cheekolu, M., Taylor, R.I., Lizarraga-Garcia, E.
2018
Manufacturers of fluid power equipment have decreased the size of hydraulic fluid reservoirs in response to economic, environmental and performance requirements. Residence times as brief as 30 seconds in mobile equipment are not unusual. Shorter fluid residence times dictate use of hydraulic fluids with improved air release characteristics. In this investigation, hydraulic fluids of the same ISO viscosity grade but varying base oil and additive composition were evaluated in a dynamometer fitted with a reservoir that incorporated an aerator at the inlet, and a mass flow meter at the outlet. The effects of aeration on piston pump efficiency and air borne noise generation were evaluated. Fluids of the same ISO viscosity grade exhibited significantly different air release rates and as a result sustained different volume fractions of entrained air. Hydraulic oils that entrained a greater volume of air demonstrated lower volumetric efficiencies and higher sound levels. Aerated fluids of the identical viscosity grade differed in volumetric efficiency by as much as 8% and perceived sound level by as much as 50%. Models for the effect of aeration on pump performance are presented.
A Fluid Property Model for Piston Pump Case Drain and Pressure Compensator Flow Losses
Conference: ASME/BATH 2015 Symposium on Fluid Power and Motion ControlMettakadapa, S., Bair, S., Aoki, S., Kobessho, M., Carter, L., Kamimura, H., Michael, P.W.
2015
This paper describes an investigation into the effects of fluid properties on piston pump flow losses through experimentation and modeling. The case drain and pressure compensator control flow rates of a variable-displacement axial piston pump were measured under a wide range of conditions. Synthetic ester, high bulk modulus, VI-improved and single grade mineral oils were evaluated. The high bulk modulus fluid exhibited 20% lower flow losses than a conventional mineral oil of the same viscosity grade. The modeling effort extended the flow loss analysis of Jeong to account for compensator control of the pump displacement. Comparisons between model predictions and measured flow losses showed good agreement. Stepwise regression analysis of the model parameters disclosed that the compressible flow term had a greater coefficient of determination than the turbulent or laminar flow terms. These findings demonstrate the potential of combining comprehensive fluid analysis with modeling to optimize fluids for the efficient transmission of power.
An Adsorption Model for the Hydraulic Motor Lubrication
Journal of TribologyMichael, P.W., Mettakadapa, S., Shahahmadi, S.
2015
This paper describes an investigation of the effects of fluid properties on hydraulic motor efficiency through experimentation and modeling. Synthetic ester, straight-grade mineral oil, and VI improved hydraulic fluids were evaluated. Fluid properties, including viscosity, shear-stability, density, and traction coefficients, were characterized. A model for relating motor mechanical efficiency to fluid properties was developed. This model combines the viscosity parameter of Stribeck with the surface adsorption model of Michaelis-Menten. The results revealed that fluids with a low traction coefficient improved the low-speed efficiency of motors by transitioning out of the boundary lubrication region at a lower Stribeck number.
An Investigation of Viscosity Effects on Axial Piston Motor Efficiency
Conference: 2014 STLE Annual Meeting & Exhibition, At Lake Buena Vista, Florida, USAMichael, P.W.
2014
This paper examines the relationship between axial piston motor efficiency and viscosity. The volumetric, mechanical, and overall efficiencies of hydraulic motors were measured under steady state conditions. Newtonian and non-Newtonian antiwear hydraulic fluids were evaluated at 50°C and 80°C. Dimensionless viscosity values for mechanical, volumetric, and overall efficiency were compared to the classic Stribeck curves. The experimental curves for volumetric and overall efficiency were consistent with the classic efficiency model. Mechanical efficiency diverged from model behavior at low Stribeck numbers; declining at low speeds and high pressures as contact conditions transitioned through the mixed-film lubrication regime. A new model for relating the viscosity to volumetric and mechanical efficiency is presented.