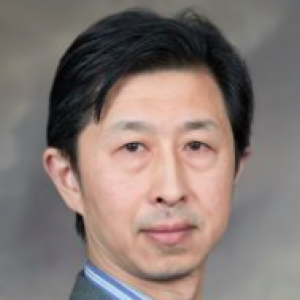
Shaowen Xu
Associate Professor, Department of Mechanical Engineering Georgia Southern University
- Statesboro GA
Shaowen Xu is an expert in Friction Stir Welding Processing, Advanced Nanomaterials and Nanofracture and Nanofailure.
Social
Biography
Areas of Expertise
Education
University of Souther Carolina
Ph.D.
Articles
Erratum to: Identification of Interaction Pressure Between Structure and Explosive with Inverse Approach
Experimental MechanicsS. Xu et al.
2011
An inverse approach for the identification of the time-dependent localized interaction pressure between a structure and an explosive has been proposed and developed. In this approach, surface measurements of structural response (displacement and velocity) are integrated with numerical simulations to identify the spatial and time-dependent interaction pressure (i.e. the normal traction) on a structure surface. For verification and validation purposes, numerical simulations are used to (a) generate the time-dependent displacement and velocity fields on the free surface of the specimen at specified time intervals, (b) form a blast wave and compute the resulting interaction traction field between the structure and blast wave on the interaction interface for comparison to inverse predictions. In particular, validation of the proposed approach was performed using numerical simulation results for an underwater explosion, with excellent agreement between the identified interaction traction and the simulation generated interaction traction up to and including the maximum traction condition. To demonstrate the potential of the method, the proposed inverse procedure was employed to estimate the interaction traction field on a thin aluminum specimen subjected to transient pressure loading through detonation of explosive buried in sand. KeywordsStructure-explosive interaction–Inverse analysis–Pressure identification–Iterated extended Kalman filter–Numerical modeling
Deformation Measurements and Material Property Estimation of Mouse Carotid Artery Using a Microstructure-Based Constitutive Model
Journal of Biomechanical EngineeringS. Xu et al.
2010
A series of pressurization and tensile loading experiments on mouse carotid arteries is performed with deformation measurements acquired during each experiment using three-dimensional digital image correlation. Using a combination of finite element analysis and a microstructure-based constitutive model to describe the response of biological tissue, the measured surface strains during pressurization, and the average axial strains during tensile loading, an inverse procedure is used to identify the optimal constitutive parameters for the mouse carotid artery. The results demonstrate that surface strain measurements can be combined with computational methods to identify material properties in a vascular tissue. Additional computational studies using the optimal material parameters for the mouse carotid artery are discussed with emphasis on the significance of the qualitative trends observed.
Evaluation of the Damage Mechanism in CFRP Composite Using Computer Vision
Journal of the Korean Society of Marine EngineeringS. Xu et al.
2010
Continuing progress in high technology has created numerous industrial applications for new advanced composite materials. Among these materials, carbon fiber-reinforced plastic (CFRP) laminate composite is typically used for low-weight carrying structures that require high specific strength. In this study, the damage mechanism of a compact tension (CT) specimen of woven CFRP laminates is described in terms of strain and displacement changes and crack growth behavior. The digital image correlation (DIC) method (which is employed here as a computer vision technique) is analyzed. Acoustic emission (AE) characteristics are also acquired during fracture tests. The results demonstrate the usefulness of these methods in evaluating the damage mechanism for woven CFRP laminate composites. From the results, we show these methods are so useful in order to evaluate the damage mechanism for woven CFRP laminate composites.
An inverse approach for pressure load identification
International Journal of Impact EngineeringS. Xu et al.
2010
An inverse approach for the identification of pressure loading on a structure has been proposed and developed. In this approach, surface measurements of structural response (e.g. strain, displacement and velocity field measurements, such as can be measured with 3D digital image correlation) are utilized as input data and are combined with numerical simulations to identify the pressure load on a structure. The inverse approach has been verified by numerical benchmarks involving pressure identification under quasi-static as well as dynamic impulse loading conditions, and also been validated by an experiment involving a quasi-static pressure load. The results indicate that the proposed inverse method can identify not only the magnitude of the quasi-static pressure but also the impulsive pressure loading history. The developed inverse approach offers an opportunity to apply inverse analysis techniques to identify interactive pressure loads (such as those resulting from a blast wave) on structures in explosive events.
Multiscale mechanical and structural characterizations of Palmetto wood for bio-inspired hierarchically structured polymer composites
Materials Science and Engineering CS. Xu et al.
2010
There has been a great deal of effort focused on engineering polymer composites with hierarchical microstructures consisting of one or more ingredients that can be organized differently across multiple length scales. However, there are hierarchical microstructures that have evolved over eons in biological materials. These unique structure–property relationships may serve as templates for engineering hierarchically structured polymer composites with tailored properties. One such biological material is the Palmetto wood of South Carolina, which was successfully used as a protective structure during the Revolutionary and Civil Wars to absorb cannon shot. Through an assembly of microfibers into macrofibers embedded in a cellulose matrix, the Palmetto wood has optimized its ability to resist failure when subjected to extreme dynamic loading events, such as hurricanes. Understanding of the dynamic and static structure–property relationship in Palmetto wood can facilitate the development of new hierarchically structured polymer composites with increased resistance to failure. Therefore, the structure–property relationship in Palmetto wood has been studied using novel multiscale microstructural and mechanical characterization techniques. Models have been developed that indicate that the hierarchical structure of Palmetto wood obeys the linear Rule-of-Mixtures across multiple length scales. This understanding has led to the development of new polymer composite structures that exhibit properties similar to Palmetto wood using conventional laminated carbon fiber–epoxy composites and new polymer nanocomposites consisting of carbon nanofibers. The use of the nanofibers appears to enhance the interaction between the composite components in a manner similar to the interaction between fibers in the Palmetto wood that enables the laminated composite to behave more like the individual layers by resisting the tendency to delaminate and increasing the Weibull statistical parameters closer to those observed in Palmetto wood.