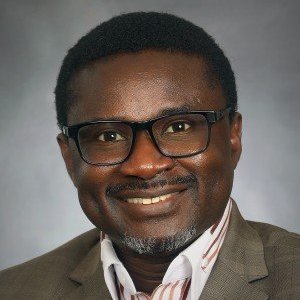
Sheku Kamara
Dean of Applied Research Milwaukee School of Engineering
- Milwaukee WI
Sheku Kamara's is an expert in additive manufacturing (3D printing) systems, materials and processes; and design for additive manufacturing.
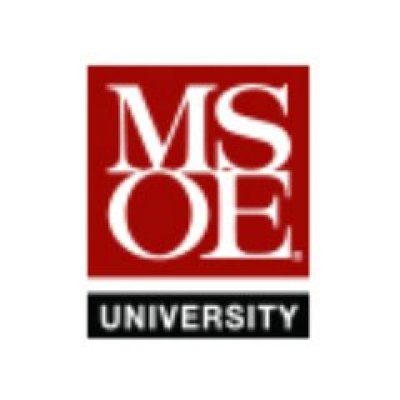
Milwaukee School of Engineering
View more experts managed by Milwaukee School of Engineering
Education, Licensure and Certification
M.S.E.
Mechanical and Electrical Engineering
MSOE
2000
B.S.M.Eng.
Mechanical Engineering
Fourah Bay College
1991
Biography
Areas of Expertise
Accomplishments
Laser Sintering DINO (Distinguished INnovator Operator Award)
2010
Additive Manufacturing Users Group
Karl O. Werwath Engineering Research Award, MSOE
2008
Affiliations
- Wisconsin Center for Manufacturing and Productivity (WCMP) : Member, Board of Directors
- Society of Manufacturing Engineers (SME) : Technical Advisor
- Association of Equipment Manufacturers (AEM) : Futures Council Member
- Additive Manufacturing Users Group (AMUG) : Past Chair
Social
Selected Publications
Material characterization studies on the laser beam formed AISI 1008 mild steel
Proceedings of the 3rd International Conference of Engineering and Applied Sciences,Kumpaty, S., Brossard, B., Kamara, S., Akinlabi, S.A., Akinlabi, E.T., Raju, G., Panda, N., Balasubramanian, K.
2014
Laser Beam Forming is a new non-contact method without the use of a die, to achieve deformation in metals, which traditionally involved the application of mechanical forces to change the shape and form of the material permanently. Laser forming causes deformation by introducing thermal stresses from an external heat source as opposed to the simple application of forces in mechanical forming. In this study, samples were formed mechanically by using a dynamic press brake machine, whereby, a punch and die apply the force. A 4.4 kW Nd:YAG laser system was used to form a second set of samples made from cold rolled AISI 1008 mild steel using laser forming. In this collaborative work involving researchers from the USA, South Africa and India, the mechanical and metallurgical properties of the unformed, mechanically formed and laser formed samples were experimentally investigated. The objective is to compare these properties amongst the different samples in order to analyze the impact of the varying methodologies especially the laser energy effects on the samples. The conclusions from these tests have provided valuable information on the applicability of laser forming to attain the appropriate surface modifications yielding the desired mechanical and metallurgical properties of the metal.
Effect of Heat Treatment on Mechanical/Metallurgical Properties of Direct Metal Laser Sintered 17-4 Precipitate Hardened Stainless Steel
Advanced Materials ResearchKumpaty, S., Kamara, S., Tomlin, B., Yoo, J., Kumpaty, H., Anderson, D., Govindaraju, M., Kanoongo, N., Balasubramanian, K.
2013
Greatbatch Medical, specializing in orthopedic implants and instruments, is currently utilizing direct metal laser sintering (DMLS) technology to develop concept prototypes. Greatbatch uses EOS GP1 Stainless Steel which adheres to the American standard for 17-4 Precipitation Hardened SS. Following DMLS, Greatbatch heat treats its parts to obtain desirable mechanical properties. In this study, three different heat treatment methods were examined: heat treatment and stress relief (HT+SR), stress relief (SR), and solution aging and annealing (SAA). The Vickers Hardness Test and the Tensile Strength Test were used to assess the mechanical properties of each sample. The research also included grain structure analysis using a Scanning Electron Microscope and surface roughness studies via profilometer measurements. For example, the HT+SR sample yielded 456 HV (hardness), an ultimate tensile strength of 1319 MPa, an yield strength of 1120 MPa, and 6.36% elongation. It was found that compared to the untreated sample, HT+SR decreased the total elongation by 73% and SAA decreased total elongation by 17% and additionally decreased hardness by 17%. It was learnt that stress relieving the part after DMLS was the superior method of choice based on its resulting mechanical properties. It was found that the grain structure of the non-treated sample resembled a solution treated sample and the stress-relieved sample actually matched an age-hardened sample. The sample that was precipitation hardened was actually over-aged. Thus it was found that the DMLS process seemed to be acting as an aging process while simultaneously building the part. Further studies in examining specific effects of DMLS and how it impacts what order heat treatments should follow would be appropriate.
Additive fabrication of custom pedorthoses for clubfoot correction
Rapid Prototyping JournalBourell, D., Stucker, B., Cook, D., Gervasi, V., Rizza, R., Kamara, S., Liu, X.C.
2010
The purpose of this paper is to determine the most‐practical means of transforming computer‐aided‐design models of custom clubfoot pedorthoses into functional pedorthoses for testing on patients in a clinical trial.