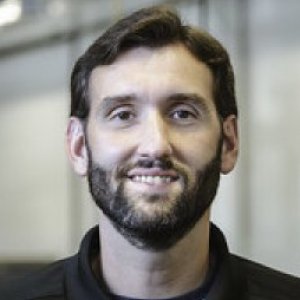
Charles Cartin, Ph.D.
Professor, Department of Mechanical and Nuclear Engineering VCU College of Engineering
- Richmond VA
Director of Makerspaces & Professor of Mechanical and Nuclear Engineering at Virginia Commonwealth University
Links
Social
Industry Expertise
Areas of Expertise
Education
Virginia Commonwealth University
Ph.D.
Engineering
2012
Virginia Commonwealth University
M.S
Mechanical Engineering
2007
Virginia Commonwealth University
B.S.
Mechanical Engineering
2006
Richard Bland College of the College of William and Mary
A.A
Computer Science
2002
Affiliations
- American Society for Engineering Education (ASEE)
- American Society of Mechanical Engineers (ASME)
- Institute of Electrical and Electronics Engineers (IEEE)
- Society of Automotive Engineers (FSAE)
Courses
Introduction to Engineering
Introduction to the engineering profession, professionalism, and ethics. Covers problem presentation, engineering calculations, digital computer applications, word processing, worksheets, programming, and elementary numerical methods.
Engineering Graphics
Presents theories and principles of orthographic projection. Studies multiview, pictorial drawings and sketches, geometric construction, sectioning, lettering, tolerancing, dimensioning and auxiliary projections. Studies the analysis and graphic presentation of space relationships of fundamental geometric elements; points, lines, planes and solids. Includes instruction in Computer Aided Drafting.
Engineering Visualization and Computation
Programming in C++ and MATLAB will be introduced. The creation and interpretation of graphical communication for engineering students. Two- and three-dimensional part and assembly representations. Dimensioning and tolerancing as a link between design and manufacturing. An introduction to solid modeling and virtual prototyping. The course will impart proficiency in computer and graphical applications of fundamental and practical importance to engineering students.
Electrical Circuits I
Teaches fundamentals of electric circuits. Includes circuit quantities of charge, current, potential, power and energy. Teaches resistive circuit analysis; Ohm's and Kirchoff's laws; nodal and mesh analysis; network theorems; RC, RL and RLC circuit transient response with constant forcing functions. Teaches AC steady-state analysis, power, three- phase circuits. Presents frequency domain analysis, resonance, Fourier series, inductively coupled circuits, Laplace transform applications, and circuit transfer functions. Introduces problem solving using computers.
Electrical Circuits I Lab
Teaches principles and operation of laboratory instruments such as VOM, electronic voltmeters, digital multimeters, oscilloscopes, counters, wave generators and power supplies. Presents application to circuit measurements, including transient and steady-state response of simple networks with laboratory applications of laws and theories of circuits plus measurement of AC quantities.
Engineering Statics
The theory and application of engineering mechanics applied to the design and analysis of rigid structures. Equilibrium of two- and three-dimensional bodies. The study of forces and their effects. Applications to engineering systems.
Dynamics and Kinematics
Kinematics and kinetics of particles. Kinematics of rigid bodies; translation and fixed-axis rotation relative to translating axes, general planar motion, fixed-point rotation and general motion. Kinetics of rigid bodies: center of mass, mass moment of inertia, product of inertia, principal-axes, parallel-axes theorems. Planar motion, work-energy method. Design of cams, gears and linkages.
Mechanics of Deformables
An introductory course covering the mechanics of deformable solids. Subjects include stress, strain and constitutive relations; bending of beams; torsion; shearing; deflection of beams; column buckling; fatigue; failure theory; analysis and design of bar-type members.
Material Science for Engineers
The study of materials from a microscopic or atomic level. Consideration of mechanical, electrical, thermal, magnetic and optical properties of metals, ceramics, polymers and composites. Thermal processing for modification of properties, dislocation and phase transformation. Material selection for design with consideration of economic, environmental and societal issues.
Solid Mechanics Lab
Experiments will be conducted on fundamental principles of solid mechanics, materials and dynamics. Topics covered include testing of materials for tensile, compression, bending and torsional loads, vibrations and material microstructure.
Mechanical Engineering Leadership
Senior/junior students will serve as lab teaching assistants in various courses associated with the mechanical and nuclear engineering department. Leadership skills will be honed as the senior/junior students guide, lead and supervise other students as they complete hands-on learning modules and/or design, conduct, analyze and report on experiments in one of these lab courses.
CAE Design
Review of geometric modeling, engineering visualization tools applicable to engineering design. Develop visual thinking and communication skills with assistance of computer modeling tools. Emphasis placed on creative design, application of physical laws, and hands-on virtual or physical projects. Topics include review of kinematics/dynamics of commonly used planar mechanisms and programming techniques for motion simulation. Interdisciplinary projects will be assigned to assess students' design knowledge.
CAE Analysis
Application of computer-aided techniques to the analysis of engineering problems utilizing linear algebra, computer calculations of matrices and numerical solution of governing differential equilibrium equations common to all fields of engineering. Students will be exposed to formulations of finite element methods of analysis. Emphasis is placed on practical aspects of structural FE modeling. Analysis programs such as ANSYS, MSC/PATRAN, MSC/NASTRAN and/or MATLAB are utilized.
Design and Additive Manufacturing
Design and additive manufacturing is the use of layer-based processes for producing parts directly from computer-aided design models without part-specific tooling. In this course students will learn about various AM technologies focusing upon their potential to support rapid prototyping and manufacturing processes coupled with the important research challenges associated with AM. This course will expand students’ knowledge in design and applied engineering as they model, fabricate, test, discuss and iterate upon mechanical 3D objects they design.
Senior Design Studio (Laboratory/Project Time)
Focus is placed upon the execution phase of the senior design (capstone) project, which meets appropriate engineering standards and multiple realistic constraints. Tasks include team meetings, brainstorming, sponsor advising, designing, fabrications, assembling, reviewing, studying, researching, testing and validating projects.
Selected Articles
Fabrication of Mechanically Strong Honeycombs with Aerogel Cores
ACS Publications - Industrial & Engineering Chemistry Research2018
Abstract:
Honeycomb aerogel composites were fabricated by reinforcing selected regions of a native aerogel matrix using photopolymerization. First, alcogels were synthesized by hydrolysis–condensation of a siloxane, and by adding a multifunctional acrylic monomer and a visible-light initiator to the gelation solution. Alcogels were then placed on a programmable translation stage and exposed to a laser. Polymerization and mechanical reinforcement were induced in the exposed regions. After exposure alcogels were dried supercritically. Thermal conductivity and out-of-plane modulus of the resulting honeycombs could be varied between values typical of native aerogels (11 mW/mK and 0.75 MPa) and those of uniformly polymerized composites (65.8 mW/mK and 36.26 MPa) by varying the translation stage speed between 2 and 3 mm/s. The results were interpreted using a rule-of-mixtures model. The mechanical properties of the composites were also investigated using finite element analysis.
Bio-Inspired Multi-Functional Drug Transport Design Concept and Simulations
Bioengineering2017
Abstract:
In this study, we developed a microdevice concept for drug/fluidic transport taking an inspiration from supramolecular motor found in biological cells. Specifically, idealized multi-functional design geometry (nozzle/diffuser/nozzle) was developed for (i) fluidic/particle transport; (ii) particle separation; and (iii) droplet generation. Several design simulations were conducted to demonstrate the working principles of the multi-functional device. The design simulations illustrate that the proposed design concept is feasible for multi-functionality. However, further experimentation and optimization studies are needed to fully evaluate the multifunctional device concept for multiple applications.
Contact Stress Modeling in Railway Bearings for Imperfect Contact Geometries
American Society of Mechanical Engineers (ASME)2015 Joint Rail Conference
Abstract:
The connection between bearing raceway condition and fatigue in tapered roller bearings utilized in the railroad environment is of interest. Roller bearings for railroad applications are typically precision ground to exact dimensions with crowned contact geometries for optimal loading of components. This normally results in completely elastic Hertzian contact stresses under standard railcar loads with original equipment manufacturer raceway contact geometries. However, with extremely uneven bogie load distributions, impact damage, corrosion and spall repair, imperfect stress distributions can occur on bearing raceways utilized in the railroad environment. Railroad bearing applications in North America have the added complexity that the life of the product is not defined in the same way as in other industries. For example, the definition of spalling remains consistent across all industries and is outlined in the Association of American Railroads (AAR) Manual of Standards and Recommended Practices. However, an inconsistency compared to other industries is that the fatigue life of the product in the rail industry is not always considered complete at the first evidence of fatigue spalling. Although some other industries allow for the remanufacture and restoration of bearing assemblies, the aggressive raceway fatigue regrinding practices allowed by the AAR are not commonly permissible in other industries. These remanufacturing practices adversely influence subsurface stress magnitudes below the raceway surface, as they reduce the effective length of the raceway and can create stress risers. Engineering tools like the novel modeling method presented in this paper can be used by bearing designers to evaluate the impact of surface discontinuities, at the center or edge of the raceway, on the overall stress state of bearing raceways.
Hertzian Contact Stress Modeling in Railway Bearings for Assorted Load Conditions and Geometries
American Society of Mechanical Engineers (ASME)2014 Joint Rail Conference
Abstract:
Increasing freight car loads demand higher performance tapered roller bearings. As the stress state on railway bearing applications continues to increase, further advancement in the modeling tools and methods used for subsurface contact stress evaluations are needed. Heat treat specifications and contact geometries for railway bearings were originally developed for ideal load conditions. However, in railroad applications, tapered roller bearings are exposed to a vast range of load conditions that are seldom perfect. Moreover, when comparing global rail markets, there are often differences in bearing loads, railcar wear conditions, maintenance practices, and reliability versus utilization expectations. Advanced modeling techniques need to be developed by bearing designers in order to meet the specific needs of each individual rail market.
Prior research has shown that subsurface stresses, resulting from rolling contact, are the primary factor in the development of fatigue cracks in railway bearings. In addition, finite element modeling software has previously been used to analyze Hertzian contact stresses under rolling contact. Recent advancements in the technology and computational power of finite element methods can be used to numerically analyze more detailed simulations of complex geometries and biased load conditions in railway bearings. These improvements in the tapered roller bearing modeling methodology are necessary to determine the material, heat treat specifications, and geometry required to meet the demands of specific railway bearing applications. Furthermore, the specific risks associated with some common railway bearing design and modeling assumptions will be evaluated. An exploratory list of these assumptions include: line versus point contact, load deflection factor, zero contact angle, rigid body assumptions, linear material behavior, neglect for overload, and uniform loading on the bearing. Emphasis will be placed on potential improvements in the theoretical and finite element prediction of surface and subsurface stresses in railway bearings under rolling contact with a review of prior research on the subject.
Design, Fabrication and Testing of a Nozzle/Diffuser PDMS Micropump with Top Actuation
Micro and Nanosystems2011
Abstract:
Micropumps with varying nozzle-diffuser geometry and actuations are being explored for many drug delivery applications. Power consumption and reliability become very critical in the realization of these micropumps. In this study, the performance of a micropump consisting of three nozzle/diffuser elements designed and fabricated from PDMS material and actuated on top by a reciprocal motor was evaluated. The performance characteristics related to the flow rate obtained from testing demonstrated the efficiency of the micropump. The results obtained illustrate the relationship between actuation frequency and fluid flow through the micropump. The effects of fluid viscosity and actuator location were also investigated and the results are presented and discussed.
Design and Fabrication of a PDMS Micropump with Moving Membranes
Proc. Univ., Gov., Ind. Micro-Nano Symp.2008
Abstract:
A novel design of a PDMS micropump with multiple vibrating membranes is being developed for applications in drug delivery and molecule sorting. The PDMS micropump consists of three nozzle/diffuser elements with vibrating membranes, which are used to create pressure difference in the pump chamber. Preliminary analysis of the fluidic characteristics of this micropump was performed using FLUENT. The transient responses of fluid velocity, pressure distributions, and flow rate during the operating cycle of the micropump were obtained. The design simulation results showed that the movement of wall membranes combined with the rectification behavior of three nozzle/diffuser elements can minimize back flow and improve net flow in one direction. Currently, the fabrication process of the micropump is being carried out. This paper will discuss in detail some of the fabrication processes that are involved in making and developing PDMS Microfluidic device.