5 min
Homes heated by human sewage could be a reality thanks to Aston University
Project to transform sewage sludge into clean water and energy awarded a share of £4.5 million by Ofwat Involves extracting energy from the waste produced during sewage and water treatment Gases obtained can be used to power engines or heat people’s homes. An Aston University project that could transform sewage sludge into clean water and energy has been awarded a share of £4.5 million by Ofwat. The University project with engineering consultancy ICMEA-UK involves extracting energy from the waste produced during sewage and water treatment and transforming it into hydrogen and/or methane. The gases can then be used to power engines or heat people’s homes. The aim is to create a sustainable and cost-efficiently run wastewater processes, plus extra energy. The initiative was one of ten winners of Ofwat’s Water Discovery Challenge, of which the Aston University scientists and two industrial partners have been awarded £427,000. Dr Jude Onwudili based at Aston University’s Energy and Bioproducts Research Institute (EBRI) is leading the team of scientists who will work with the partners to develop a trial rig to transform solid residues from wastewater treatment plants to hydrogen and/or methane. The two-stage process will involve the initial transformation of organic components in the sludge into liquid intermediates, which will then be converted to the fuel gases in a second stage. The project is called REvAR (Renewable Energy via Aqueous-phase Reforming), and Dr Onwudili will be working with lead partner and engineering consultancy company ICMEA-UK Limited and sustainable infrastructure company Costain. REVAR combines the use of hot-pressurised water or hydrothermal conditions with catalysts to achieve high conversion efficiency. The technique can treat sewage sludge in just minutes, and it is hoped that it will replace existing processes. In 2013, a Chartered Institution of Water and Environmental Management report stated that the sector is the fourth most energy intensive industry in the UK. Dr Onwudili said: “This project is important because millions of tonnes of sewage sludge are generated in the UK each year and the water industry is struggling with how to effectively manage them as waste. “Instead, they can be converted into valuable feedstocks which are used for producing renewable fuel gases, thereby increasing the availability of feedstocks to meet UK decarbonisation targets through bioenergy. “We will be taking a waste product and recovering two important products from it: clean water and renewable energy. Overall, the novel technology will contribute towards meeting UK Net Zero obligations by 2050 and ties in with the University’s purpose to make our world a better place through education, research and innovation.” The Water Discovery Challenge aims to accelerate the development and adoption of promising new innovations for the water sector. Over the next six months, winners will also receive non-financial support and will be able to pitch their projects to potential water company partners and/or investors. The 10 winning teams are from outside the water industry and were chosen because of their projects’ potential to help solve the biggest challenges facing the sector. The competition is part of the Ofwat Innovation Fund, run by the water regulator Ofwat, with Challenge Works, Arup and Isle Utilities and is the first in the water sector to invite ideas from innovators across industries. Helen Campbell, senior director for sector performance at Ofwat, said: “This competition was about reaching new innovators from outside the sector with different approaches and new ideas, and that’s exactly what the winners are doing. “The products and ideas recognised in this cross-sector challenge will equip water companies to better face challenges of the future – including achieving sustainability goals and meeting net zero targets – all while providing the highest-quality product for consumers.” ENDS A Blueprint For Carbon Emissions Reduction in the UK Water Industry The Chartered Institution of Water and Environmental Management https://www.ciwem.org/assets/pdf/Policy/Reports/A-Blueprint-for-carbon-emissions-reductions-in-the-water-industry.pdf Ofwat Innovation Fund Ofwat, the Water Services Regulation Authority for England and Wales, has established a £200 million Innovation Fund to grow the water sector’s capacity to innovate, enabling it to better meet the evolving needs of customers, society and the environment. The Innovation Fund, delivered in partnership with Challenge Works (formerly known as Nesta Challenges) and supported by Arup and Isle Utilities, is designed to complement Ofwat’s existing approach to innovation and to help deliver against Ofwat’s strategy which highlights the role of innovation in meeting many of the challenges the sector faces. About ICMEA-UK Based in Sheffield, in the North of England, ICMEA-UK is the UK arm of an established Italian innovative engineering company ICMEA SRL. They are an innovative Engineering consultancy company, and work in partnership with a range of other organisations to provide innovative, bespoke solutions to problems where an Engineering solution is required. About Costain Costain helps to improve people’s lives by creating connected, sustainable infrastructure that enables people and the planet thrive. They shape, create, and deliver pioneering solutions that transform the performance of the infrastructure ecosystem across the UK’s energy, water, transportation, and defence markets. They are organised around their customers anticipating and solving challenges and helping to improve performance. By bringing together their unique mix of construction, consulting, and digital experts they engineer and deliver sustainable, efficient, and practical solutions. About Aston University For over a century, Aston University’s enduring purpose has been to make our world a better place through education, research and innovation, by enabling our students to succeed in work and life, and by supporting our communities to thrive economically, socially and culturally. Aston University’s history has been intertwined with the history of Birmingham, a remarkable city that once was the heartland of the Industrial Revolution and the manufacturing powerhouse of the world. Born out of the First Industrial Revolution, Aston University has a proud and distinct heritage dating back to our formation as the School of Metallurgy in 1875, the first UK College of Technology in 1951, gaining university status by Royal Charter in 1966, and becoming The Guardian University of the Year in 2020. Building on our outstanding past, we are now defining our place and role in the Fourth Industrial Revolution (and beyond) within a rapidly changing world. For media inquiries in relation to this release, contact Nicola Jones, Press and Communications Manager, on (+44) 7825 342091 or email: n.jones6@aston.ac.uk
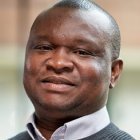